Apariția mașinilor -unelte CNC este o manifestare a unui progres mare în industrie. Poate rezolva mai bine problemele de prelucrare a pieselor dezordonate, fine, mici și modificabile. Este o mașină -unelte automată sensibilă și eficientă. Când programatorii folosesc mașini -unelte CNC pentru procesare, aceștia trebuie să analizeze mai întâi procesul. Conform informațiilor, forma generalizată, precizia prelucrării etc. a piesei de lucru care trebuie procesate, este selectată o mașină -unelte adecvată, planul de procesare este întocmit, secvența de procesare a pieselor este confirmată, instrumentele utilizate în fiecare proces, Aparatul și cantitatea de tăiere etc.
1. Selectarea rezonabilă a mașinilor -unelte
Atunci când prelucrați piese pe o mașină -unelte CNC, există în general două situații.
Prima situație: există un model de parte și un gol și trebuie selectată o mașină -unelte CNC potrivită pentru procesarea piesei.
A doua situație: există deja o mașină -instrument CNC și este necesară selectarea pieselor potrivite pentru procesarea pe mașină -instrument.
Indiferent de situație, principalii factori de luat în considerare sunt informațiile și tipul semifabricatului, gradul de tulburare în forma generalizată a piesei, dimensiunea scării, precizia de procesare, numărul de piese și tratamentul termic cerințe. În rezumat, există trei puncte:
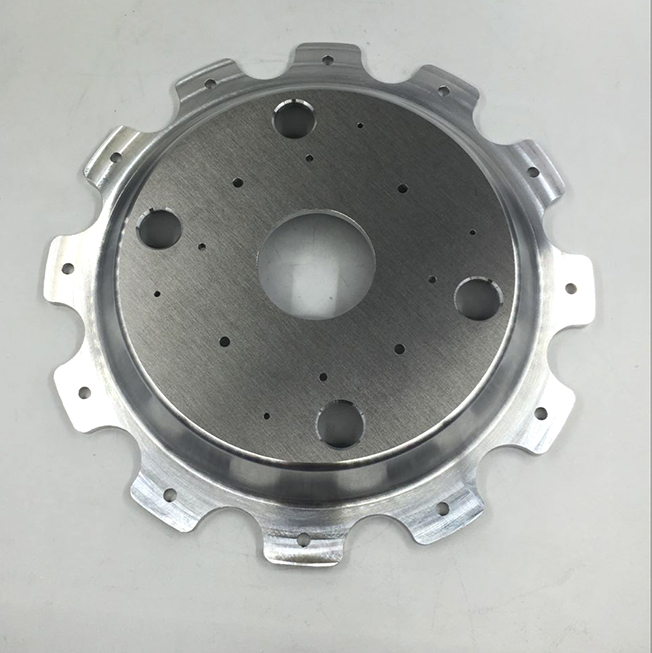
① Este necesar să vă asigurați cerințele de abilități pentru procesarea pieselor și procesarea produselor calificate.
② Conduți pentru îmbunătățirea ratei de producție.
Reduceți cât mai mult costurile de producție (costurile de procesare).
2. Analiza tehnologiei pieselor de prelucrare CNC
Analiza tehnică a prelucrării CNC implică o gamă largă de zone, astfel încât o analizăm doar din cele două aspecte ale posibilității și comodității prelucrării CNC.
(1) Datele de scară din desenul piesei ar trebui să se conformeze principiului comodității de programare
1. Metoda de indicație a dimensiunii pe desenul piesei trebuie utilizată pentru caracteristicile prelucrării CNC. În ceea ce privește desenul de prelucrare CNC, scara ar trebui să fie citată cu aceeași date sau scara de coordonate ar trebui să fie dată direct. Această metodă de marcare nu numai că facilitează programarea, dar facilitează și coordonarea dintre standarde și aduce o mare comoditate în respectarea consistenței de referință de proiectare, a referințelor de proces, a reperelor de inspecție și a setărilor de origine a programării. Deoarece proiectanții de piese iau în considerare, în general, asamblarea și alte caracteristici de utilizare în etichetarea la scară, trebuie să aleagă metode parțiale de etichetare, ceea ce va aduce o mulțime de inconveniente pentru organizarea procesului și prelucrarea CNC. Deoarece precizia prelucrării CNC și precizia poziționării repetate sunt foarte mari, caracteristicile de utilizare nu vor fi deteriorate din cauza erorilor mari de acumulare, astfel încât o parte din metoda de etichetare împrăștiată poate fi modificată la aceeași scară de citare de referință sau metoda de etichetare care oferă direct coordonate scară. .
2. Condițiile mai multor elemente care constituie inducția piesei ar trebui să fie suficiente
Coordonatele punctului de bază sau nodului trebuie calculate în timpul programării manuale. În timpul programării active, ar trebui definite toate elementele genomice care constituie o parte. Prin urmare, atunci când analizăm desenul piesei, este necesar să se analizeze dacă condițiile date ale puținelor elemente sunt suficiente. De exemplu, arcul și linia dreaptă, arcul și arcul sunt tangente pe desen, dar în funcție de scala dată pe desen, atunci când condiția de tangență este calculată, devine starea de intersecție sau separare. Din cauza condițiilor insuficiente ale elementelor constitutive, este imposibil să începeți programarea. Când întâlniți această situație, aceasta ar trebui rezolvată prin consultarea cu proiectantul piesei.
(2) Structura și măiestria fiecărei părți de procesare a piesei ar trebui să se conformeze caracteristicilor prelucrării CNC
1) Cel mai bine este să selectați același tip și dimensiune de geometrie pentru cavitatea și forma părților. Acest lucru poate reduce specificațiile instrumentului și numărul de modificări ale instrumentelor, poate facilita programarea și poate îmbunătăți eficiența producției.
2) Mărimea filei a canelurii interioare determină dimensiunea diametrului sculei, astfel încât raza filei a canelurii interioare nu ar trebui să fie prea mică. Procesarea pieselor este legată de înălțimea rezumării procesate, de dimensiunea razei arcului de transfer și așa mai departe.
3) Atunci când piesa frecă planul de jos, raza filei de jos a canelurii R nu ar trebui să fie prea mare.
4) Trebuie utilizată o poziționare constantă de referință. În prelucrarea CNC, dacă nu există o poziționare constantă de referință, reinstalarea piesei va provoca inconsecvența în orientarea și scara celor două fețe după prelucrare. Prin urmare, pentru a evita apariția problemelor menționate mai sus și pentru a asigura exactitatea orientării relative după cele două procese de prindere, ar trebui selectată o poziționare constantă de referință.
Cel mai bine este să aveți găuri adecvate pe părți ca găuri de referință de poziționare. Dacă nu, setați găurile procesului ca găuri de referință de poziționare (cum ar fi adăugarea de bagaje de proces pe gol sau setarea găurilor procesului pe marjă pentru a fi măcinate în procesul ulterior). Dacă gaura procesului nu poate fi făcută, cel puțin aspectul finit ar trebui utilizat ca un punct de referință consistent pentru a reduce erorile cauzate de cele două prinderi. În plus, ar trebui să analizeze, de asemenea, dacă pot fi asigurate exactitatea prelucrării și toleranțele dimensionale ale părților, dacă există dimensiuni redundante care provoacă contradicții sau dimensiuni închise care afectează organizarea procesului.